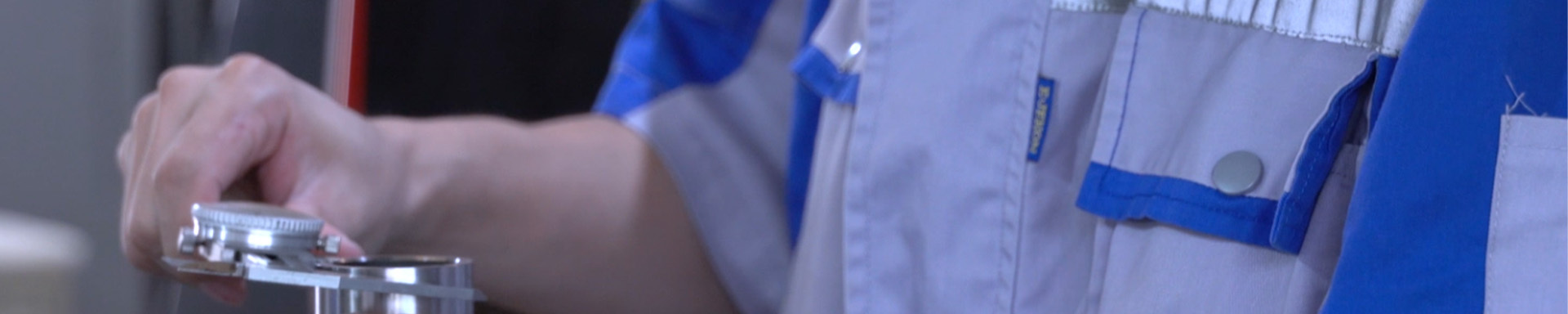
Warum sind Kobaltlegierungen in Vulkanisierungsumgebungen mit hohen Temperaturen besser als Nickellegierungen?
2025-03-26 09:00In Hochtemperatur-Vulkanisationsumgebungen hat die Materialwahl direkten Einfluss auf die Lebensdauer und Stabilität der Anlage. Kobaltlegierungen sind vielen herkömmlichen Nickellegierungen unter extremen Bedingungen aufgrund ihrer hervorragenden Hochtemperaturbeständigkeit, Verschleißfestigkeit, Schlagfestigkeit und Korrosionsbeständigkeit überlegen. Was also verschafft Kobaltlegierungen einen Vorteil in Hochtemperatur-Vulkanisationsumgebungen?
1. Hochtemperaturstabilität von Kobaltlegierungen
Kobaltlegierungen wie Alloy 6K behalten ihre hohe Festigkeit und Härte unter 900 °C bei, was ihnen gute mechanische Eigenschaften in Hochtemperaturumgebungen verleiht. Ihre hervorragende Oxidationsbeständigkeit bei hohen Temperaturen beruht hauptsächlich auf der schützenden Oxidschicht aus Chrom, die der Erosion durch Hochtemperaturgase, Sulfide und andere korrosive Medien wirksam widersteht.
Im Gegensatz dazu weisen Nickellegierungen zwar auch bei hohen Temperaturen eine gewisse Vulkanisationsbeständigkeit auf, sind jedoch auf die synergistische Wirkung von Elementen wie Aluminium und Molybdän angewiesen, die unter bestimmten rauen Betriebsbedingungen zu Leistungseinbußen führen kann. Kobaltlegierungen sind daher unter dauerhaft hohen Vulkanisationstemperaturen stabiler.
2. Hervorragende Verschleiß- und Schlagfestigkeit
Kobaltlegierungen zeichnen sich aufgrund ihrer einzigartigen, gleichmäßig verteilten Karbidstruktur durch hohe Beanspruchung, Partikelauswaschung und Gleitreibung aus und reduzieren den Bauteilverschleiß deutlich. Insbesondere in sulfidischen Hochtemperaturatmosphären, wo die Verschleißfestigkeit vieler Werkstoffe deutlich abnimmt, weisen Kobaltlegierungen weiterhin niedrige Verschleißraten auf.
Darüber hinaus bietet die Zähigkeit der Kobaltmatrix eine hervorragende Schlagfestigkeit gegen Ermüdungsschäden durch Wechselbelastung mechanischer Komponenten. Diese Eigenschaft macht Kobaltlegierungen zu einem idealen Werkstoff für die Herstellung hochtemperaturbeständiger Verschleißteile wie Ventilsitze, Lagerbuchsen, Laufräder und Dichtringe.
3. Ausgezeichnete Korrosions- und Oxidationsbeständigkeit
Der hohe Chromgehalt der Kobaltlegierung sorgt dafür, dass sie in sauren Lösungen, Seewasser und Vulkanisationsumgebungen mit hohen Temperaturen stabil bleibt und eine hohe Korrosionsbeständigkeit gegenüber Salpetersäure, organischen Säuren und anderen chemischen Medien aufweist.
Unter Hochtemperaturvulkanisationsbedingungen wirken Sulfide extrem aggressiv auf Materialien, und viele Metalle sind anfällig für Sulfidkorrosion oder sogar Bruch. Kobaltlegierungen können jedoch aufgrund ihrer speziellen Zusammensetzung der Sulfidatmosphäre bei hohen Temperaturen wirksam widerstehen und finden breite Anwendung in chemischen Reaktoren, Schiffsausrüstung, Erdölraffinerien, Gasturbinen und anderen Bereichen.
Obwohl die Korrosionsbeständigkeit von Nickellegierungen besser ist als die vieler gängiger Metalle, ist die Korrosionsbeständigkeit bestimmter Nickellegierungen in einer Hochtemperatur-Sulfidumgebung immer noch begrenzt, was es schwierig macht, die Anforderungen an einen langzeitstabilen Betrieb zu erfüllen.
4. Optimierte Balance zwischen Zusammensetzung und Prozess
Kobaltlegierungen erreichen durch die präzise Steuerung des Verhältnisses von Kobalt, Chrom, Wolfram, Kohlenstoff und anderen Elementen ein Gleichgewicht zwischen Hochtemperaturbeständigkeit, Verschleißfestigkeit und Korrosionsbeständigkeit. Diese Materialkonstruktion ermöglicht eine hervorragende Gesamtleistung unter extremen Arbeitsbedingungen und wird daher häufig in der Luft- und Raumfahrt, im Energiesektor, in der Petrochemie, in der Stahlverhüttung sowie in Hochtemperatur- und Hochdruckventilen eingesetzt.
Im Gegensatz dazu zeichnen sich Nickellegierungen zwar durch ihre hohe Festigkeit, ihren niedrigen Wärmeausdehnungskoeffizienten und ihre hervorragenden elektromagnetischen Eigenschaften bei bestimmten Anwendungen aus, sind jedoch in vulkanisierten Umgebungen mit hohen Temperaturen weniger abrieb- und stoßfest und ihre Gesamtleistung ist weniger stabil als bei Kobaltlegierungen.
Fazit: Warum Kobaltlegierungen?
Zusammengefasst sind Kobaltlegierungen Nickellegierungen in Hochtemperatur-Vulkanisationsumgebungen überlegen und bieten folgende Hauptvorteile:
✅ Höhere Hochtemperaturstabilität – hält hohen Temperaturen bis zu 900 °C stand und die mechanischen Eigenschaften bleiben stabil.
✅ Bessere Verschleißfestigkeit – Die Karbide sind gleichmäßig verteilt, sodass sie in Umgebungen mit Reibungsverschleiß hervorragende Leistungen erbringen.
✅ Bessere Schlagfestigkeit – Die Kobaltmatrix verleiht dem Material eine gute Ermüdungs- und Schlagfestigkeit.
✅ Überlegene Korrosionsbeständigkeit – Hervorragende Korrosionsbeständigkeit bleibt bei Vulkanisation bei hohen Temperaturen sowie in sauren und marinen Umgebungen erhalten.
✅ Wissenschaftlich optimierte Zusammensetzung – Erzielt ein Gleichgewicht der Eigenschaften zwischen Hitze-, Verschleiß- und Korrosionsbeständigkeit.
Daher ist Kobaltlegierung eine zuverlässigere Wahl für harte Arbeitsbedingungen, die hohe Temperaturbeständigkeit, Verschleiß- und Korrosionsbeständigkeit erfordern, und wird häufig in kritischen Bereichen wie der chemischen Industrie, der Energiebranche, der Metallurgie und der Luft- und Raumfahrt eingesetzt.
Wenn Sie auf der Suche nach Hochleistungsmaterialien aus Kobaltlegierungen sind, kontaktieren Sie uns gerne. SYTOP bietet qualitativ hochwertige Kobaltlegierungsprodukte, die Ihren speziellen Anforderungen gerecht werden!