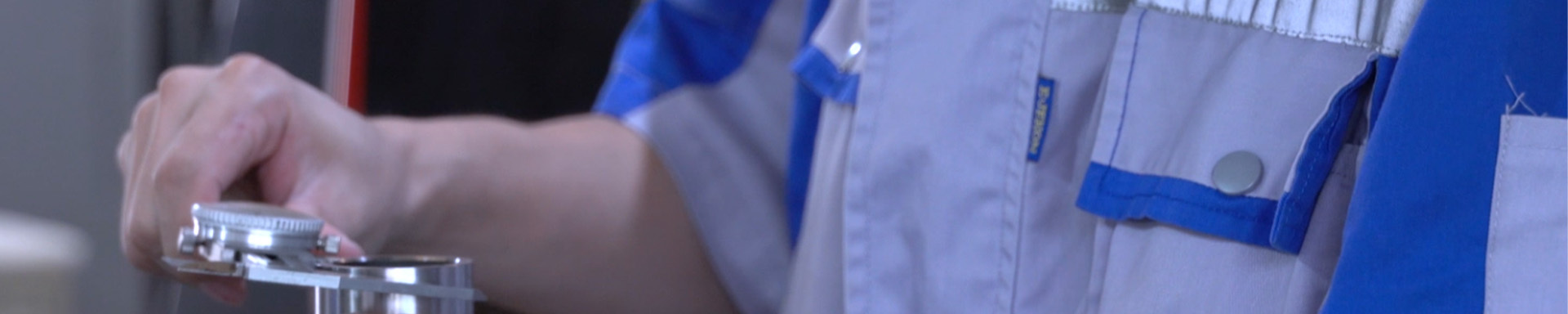
Warum sollten Sie sich bei der Ventilreparatur für Schweißzusätze aus Kobaltlegierungen entscheiden?
2025-03-13 09:00In der modernen Industrie und im Transportwesen sind Ventile als Kernkomponenten von Motoren über lange Zeit hohen Temperaturen, hohem Druck und korrosiven Medien ausgesetzt. Laut Statistik der International Automobile Maintenance Association (IAMA) aus dem Jahr 2024 sind Ventilausfälle für 35 % der Motorreparaturfälle verantwortlich. Die Wahl des Reparaturmaterials wirkt sich direkt auf die Lebensdauer und Betriebssicherheit der Anlage aus. Basierend auf materialwissenschaftlicher Forschung und Daten aus der Industriepraxis analysiert dieser Artikel die technischen Vorteile von Schweißzusätzen aus Kobaltlegierungen bei der Ventilreparatur.
Die zentralen Herausforderungen der Klappenreparatur
Extreme Arbeitsbedingungen führen zu Materialverlust
Ventile von Verbrennungsmotoren arbeiten bei Temperaturen von bis zu 800–1000 °C, während Turboladerventile Temperaturen von über 1200 °C erreichen und dabei Gasdrücken von bis zu 20 MPa standhalten (Quelle: SAE International „Engine Materials Reliability Study“). Herkömmliche Schweißzusätze aus Edelstahl sind in dieser Umgebung anfällig für thermische Ermüdung und oxidative Korrosion.
Chemischer Angriff und Verschleiß
Säuren aus der Verbrennung schwefelhaltiger Kraftstoffe sowie alkalische Bestandteile in Schmierflüssigkeiten beschleunigen die galvanische Korrosion von Ventiloberflächen. Tests der American Society for Testing and Materials (ASTM) zeigen, dass die jährliche Korrosionsrate von gewöhnlichem legiertem Stahl in einer sauren Umgebung 0,3 mm erreicht (ASTM G1-03-Standard).
Technische Durchbrüche bei Schweißzusätzen aus Kobaltlegierungen
Hochtemperaturleistung
Kobaltbasierte Legierungen haben eine Festphasenlinientemperatur von über 1320 °C, deutlich höher als die von nickelbasierten Legierungen (~1260 °C) und Edelstahl (~1370 °C, jedoch mit geringerer Oxidationsbeständigkeit).
Korrosions- und Verschleißbeständigkeitseigenschaften
In Tests, die Motorabgase (mit SO₂ und NOx) simulieren, weisen Kobaltlegierungen ein Lochfraßpotenzial von +0,8 V (gegenüber SCE) auf, das 45 % höher ist als bei Edelstahl 316L (Quelle: Society of Corrosion Engineers NACE TM0177-2016). Ihre Rockwellhärte (HRC 38–60) bietet eine fünfmal höhere Verschleißfestigkeit als gewöhnlicher Kohlenstoffstahl (ISO 7124).
Angepasste thermomechanische Eigenschaften
Der Wärmeausdehnungskoeffizient der Kobaltlegierung (13,5×10⁻⁶/°C) ist sehr gut mit Materialien kompatibel, die üblicherweise für Ventile verwendet werden (z. B. hitzebeständiger Stahl 21-4N), wodurch die Restspannung nach dem Schweißen reduziert wird.
Anwendungsüberprüfung
Reparatur von Schwerlast-Lkw-Ventilen
Trackingdaten eines Logistikunternehmens zu 100 Dieselmotoren zeigen, dass die durchschnittliche Lebensdauer von Ventilen, die mit Schweißzusätzen auf Kobaltbasis repariert wurden, 120.000 Kilometer erreicht und damit 42 % länger ist als die von Ventilen, die mit herkömmlichen Schweißzusätzen auf Nickelbasis repariert wurden (Datenquelle: Bericht 2024 der China Road Transportation Association).
Wartung von Flugzeugtriebwerken
Pratt & Whitney verwendete bei der Reparatur der Ventile des PW1100G-Triebwerks Schweißzusätze auf Kobaltbasis und bestand die von der FAA zugelassenen Ermüdungstests mit einer um 35 % reduzierten Rissausbreitungsrate (FAA AC 33.71-1A).
Auswahlkriterien für Schweißzusätze aus Kobaltlegierungen
Prozesskompatibilität
Schweißzusätze auf Kobaltbasis unterstützen WIG-, MIG- und Laserschweißen mit einem breiten Spektrum an Schweißströmen (80–200 A) und eignen sich für die Präzisionsreparatur von Ventilen mit φ8–φ50 mm (Standard AWS A5.11/A5.11M:2021).
Kosteneffizienz
Die Kosten für eine einzelne Reparatur sind 25 % höher als bei Schweißzusätzen auf Nickelbasis, die Gesamtkosten über den gesamten Lebenszyklus sind jedoch 38 % niedriger (basierend auf dem LCC-Lebenszykluskostenmodell, Daten aus dem Industrial Maintenance Cost Optimization Report 2023 von McKinsey).
Branchentrends und Innovationsrichtungen
Anpassung von Fahrzeugen mit neuer Energie
Das Patent für den Wasserstoff-Brennstoffzellenmotor 2024 von Toyota zeigt, dass eine Beschichtung aus einer Legierung auf Kobaltbasis die Haltbarkeit der Ventile bei extremen Temperaturschwankungen von -40 °C bis 85 °C verbessert (WO2024/037896A1).
Fortschritte bei Umweltprozessen
Die neueste Plasma-Overlay-Technologie reduziert die Spritzerrate von Schweißzusätzen auf Kobaltbasis auf weniger als 2 % und entspricht damit der EU-Richtlinie RoHS 2.0 (2015/863/EU).
Abschluss
Schweißzusätze aus Kobaltlegierungen haben sich aufgrund ihrer einzigartigen Hochtemperaturbeständigkeit, Korrosionsbeständigkeit und mechanischen Eigenschaften zum Maßstab in der Ventilreparatur entwickelt. Durch die Integration von 3D-Drucktechnologie und Kobaltmatrix-Verbundwerkstoffen wird die Ventilreparatur künftig präziser und kostengünstiger.