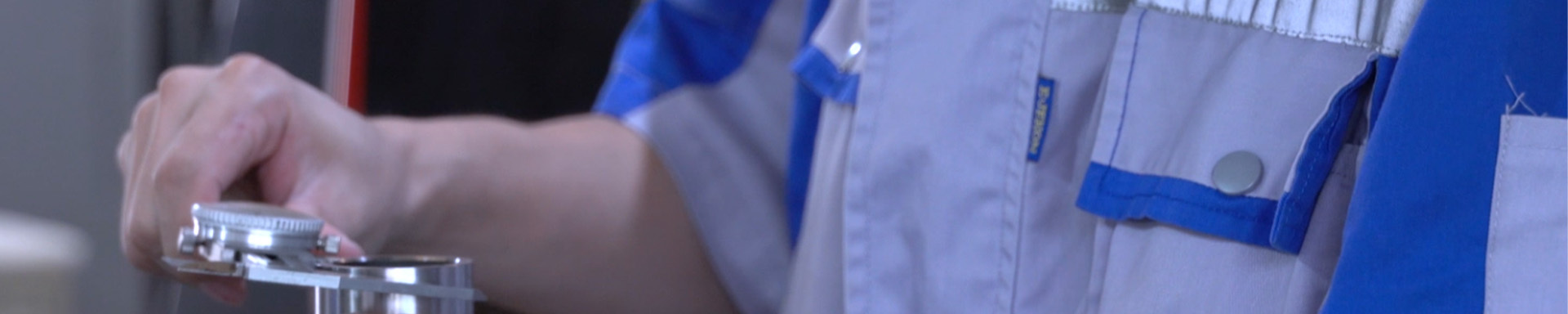
Stellite 21/ AMS5385G UNS R30021
2021-09-06 10:52Die Legierung Stellite 21 CoCrMo (Kobalt-Chrom-Molybdän) gehört zu den Legierungen auf Kobaltbasis und ist auch eine Art der sogenannten Stellite-Legierung. Es ist eine Legierung auf Kobaltbasis mit ausgezeichneter Verschleißfestigkeit und Korrosionsbeständigkeit. Die erste auf Kobalt basierende Legierung war eine binäre Kobalt-Chrom-Legierung, und dann wurde sie zu einer ternären Kobalt-Chrom-Wolfram-Zusammensetzung entwickelt, und später wurde dann eine Kobalt-Chrom-Molybdän-Legierung entwickelt. Kobalt-Chrom-Molybdän-Legierung ist eine Legierungsart mit Kobalt als Hauptbestandteil, die einen erheblichen Anteil an Chrom, Molybdän und einen geringen Anteil an Nickel, Kohlenstoff und anderen Legierungselementen enthält und gelegentlich auch Eisen enthält. Je nach Zusammensetzung der Legierung können sie zu Schweißdraht verarbeitet werden, das Pulver kann zum Hartschweißen, thermischen Spritzen,
Kobalt und Chrom sind die beiden Grundelemente von Legierungen auf Kobaltbasis, und die Zugabe von Molybdän kann feinere Körner erhalten und nach dem Gießen oder Gießen eine höhere Festigkeit aufweisen. Kobalt-Chrom-Molybdän-Legierungen werden grundsätzlich in zwei Kategorien eingeteilt: CoCrMo-Legierungen, bei denen es sich in der Regel um Gussprodukte handelt, und CoNiCrMo-Legierungen, bei denen es sich in der Regel um (warm)gegossene Präzisionsbearbeitungen handelt. Die gegossene CoCrMo-Legierung wird seit Jahrzehnten in der Zahnheilkunde verwendet und wird heute zur Herstellung künstlicher Gelenke verwendet. Die gegossene CoNiCrMo-Legierung wird verwendet, um Gelenke herzustellen, die schwere Lasten aufnehmen, wie Kniegelenke und Hüftgelenke. Als Gelenkimplantatmaterial setzt die CoCrMo-Legierung jedoch Co, Cr, Ni und andere schädliche Ionen frei, nachdem sie in den menschlichen Körper implantiert wurde.
Chemische Zusammensetzung von Stellit 21:
Mechanische Eigenschaften von Stellit 21:
Schweißbarkeitsanalyse
Nach aktueller, international ausgereifter Erfahrung wird die Funktion der Auftragungsschicht hauptsächlich durch die chemische Zusammensetzung und Verdünnungsrate des Schweißgutes der Auftragungsschicht bestimmt, wobei die chemische Zusammensetzung des Schweißgutes von der chemischen Zusammensetzung des Schweißgutes abhängt . Bei Auswahl des Schweißmaterials Danach wurde die chemische Zusammensetzung des Schweißgutes grundsätzlich bestätigt. Bei der Auswahl des Schweißverfahrens ist darauf zu achten, dass externe Faktoren keine Veränderungen der chemischen Zusammensetzung des Schweißguts oder das Eindringen anderer Fremdkörper verursachen; die Größe der Verdünnungsrate hängt von der Größe des Wärmeeintrags (E) beim Schweißen ab, dh Wärme Je größer der Eintrag, desto höher die Verdünnungsrate; andernfalls wird die Abnahme und der Wärmeeintrag wie folgt berechnet:
In der Formel: E ist die Schweißwärmezufuhr, J/mm; I ist der Schweißstrom A; U ist die Schweißspannung, V; u ist die Schweißgeschwindigkeit, mm/min. Daher ist es bei der Auswahl des Schweißverfahrens erforderlich, die chemische Zusammensetzung des Schweißguts der Auftragsschicht sicherzustellen und den Schweißwärmeeintrag zu reduzieren. Der vorbestätigte Prozessablauf ist wie folgt: Stanzen→Hobeln und Fräsen – Zerstörungsfreie Prüfung (PT)→Vorwärmen→Schweißen→Sichtprüfung→Zerstörungsfreie Prüfung (PT)→Probenbearbeitung→Chemische Analyse und Funktionsprüfung→Materialsammlung→Ergebnisanalyse → Aufräumen melden und Produktion verwenden (5) 0
Anforderungen vor dem Schweißen
Nachdem durch Einweichen der Flüssigkeit bestätigt wurde, dass die Oberfläche des Auftragsschweißens frei von Rissen, Poren, Zwischenschichten, schwerem Leder und anderen Oberflächenfehlern ist, reinigen Sie die Oberfläche des Auftragsschweißens mit Aceton. Zum Auftragschweißen hochwertiger Materialien die Auftragschweißteile auf über 15°C vorwärmen. Nachdem sich die Hand berührt und warm angefühlt hat, wird das Schweißen sofort durchgeführt. Stellen Sie gleichzeitig sicher, dass die relative Luftfeuchtigkeit der Schweißumgebung nicht höher als 80 % ist, die Windgeschwindigkeit nicht höher als 2 m/s ist und die Reinheit des Ar-Gases 99,99 % erreichen muss
Anforderungen beim Schweißen
Aus der Berechnungsformel lässt sich erkennen, dass die Größe der Schweißwärmezufuhr (E) proportional zur Größe des Produkts aus Schweißstrom (I) und Schweißspannung (U) und der Größe der Schweißgeschwindigkeit ( v) ist umgekehrt proportional. Für das manuelle Argon-Wolfram-Lichtbogenschweißverfahren (GTAW) mit nicht schmelzender Elektrode wird der Schweißstrom den voreingestellten steuerbaren Elementen zugeordnet, und die Schweißspannung und die Schweißgeschwindigkeit werden den künstlichen Steuer- und Zufallselementen zugeordnet. Dies steht im vierten Teil der französischen RCC-M-Spezifikation. Zitiert in Band S"Schweißen". Gleichzeitig ist es in Abschnitt 8.5.4 von ISO 15614-7:2007 beschrieben"Qualifizierung von Schweißverfahren für metallische Werkstoffe Teil 7: Auftragsschweißen": Die Obergrenze des zugelassenen Wärmeeintragsbereichs für jede Schicht liegt außerhalb der Bewertung des Schweißverfahrens. Der Wärmeeintrag der gleichen Schicht beträgt 25 % und die untere Grenze liegt bei weniger als 10 % der Wärmezufuhr der gleichen Schicht bei der Bewertung des Schweißprozesses.
Da die Schweißspannung und Schweißgeschwindigkeit vom Menschen gesteuert werden, liegt bei der Auswahl der Schweißspezifikationsparameter die Priorität auf der Steuerung der Schweißstromstärke. Wählen Sie unter der Prämisse, die Qualität des Auftragsschweißens zu gewährleisten, einen möglichst niedrigeren Schweißstromwert, nämlich Choose"Kleinstrom, Kurzlichtbogenschweißen, schnelles, mehrlagiges Mehrlagenschweißen". Seine Schweißspezifikationsparametereinstellung. Kontrollieren Sie den Raupenabstand während des Auftragsschweißens streng. Die nächste Perle sollte auf die halbe Breite der vorherigen Perle gedrückt werden, um die Verdünnungsrate zu minimieren. Die Schweißrichtung zwischen den Schweißlagen sollte nacheinander hin und her geschweißt werden, um Schweißspannungen und Verformungen zu reduzieren. Vor dem Schweißen sollte die Schweißstromquelle vorab auf den Schutzzustand von Argon-Vorgas und Argon-Gas verzögert eingestellt werden. Zu Beginn sollte der Strom an der Zündlichtbogenplatine aus dem gleichen Material eingestellt, der Lichtbogen gezündet und dann das Schweißen zum Beginn des Schweißbereichs übertragen werden, um mit dem Schweißen zu beginnen. Ausgehend von der nummerierten Position Nr. 6 entlang der Mittelachse der Schweißnaht wird die Schweißnaht beidseitig hin und her geschweißt. Der Krater muss beim Schließen des Lichtbogens gefüllt werden, um das Auftreten von Kraterrissen zu vermeiden. Schweißverbindungen verwenden das Reflow-Lichtbogenverfahren, um die Qualität der Verbindungen an den Schweißnähten sicherzustellen. Die Schweißnähte zwischen den einzelnen Schweißnähten müssen versetzt sein. Die Oberflächendicke sollte im Bereich von 3,5 bis 4,0 mm liegen. Nach dem Schweißen mit Steinwolle warm halten und langsam auf Raumtemperatur abkühlen.
Schweißnachteile und Maßnahmen
Aussehensveredelung vor und während des Schweißens. Entfernen Sie gründlich den Oberflächenoxidbelag, Ölflecken, Verunreinigungen, Zwischenschichten, geschmolzene Schlacke und andere schädliche Verunreinigungen, um sicherzustellen, dass die Oberflächenoberfläche glatt und geschmiert ist, mit metallischem Glanz und ohne Fehler wie Risse, Poren, Schlackeneinschlüsse usw. an der Oberfläche;
Temperaturkontrolle während des Schweißens, einschließlich Vorwärmen vor dem Schweißen, Temperaturkontrolle zwischen den Durchgängen und langsames Abkühlen nach dem Schweißen. Vorwärmen vor dem Schweißen und langsames Abkühlen nach dem Schweißen können die Abkühlgeschwindigkeit nach dem Schweißen reduzieren und einen Teil der durch schädlichen Temperaturgradienten verursachten Eigenspannung reduzieren; Zwischenlagen-Temperaturregelung kann die Hochtemperatur-Verweilzeit verkürzen, die grobe Kristallversprödung der Schweißverbindung verhindern und die Schlagzähigkeit verringern;
Spannungsarmglühende Wärmebehandlung nach dem Schweißen. Nachdem die Oberflächenbehandlung abgeschlossen ist, ist die innere Zwangsspannung groß, was einfach eine Rissbildung verursacht. Durch die spannungsarme Wärmebehandlung kann die Eigenspannung rechtzeitig beseitigt werden, um das Auftreten von Fehlern zu vermeiden.