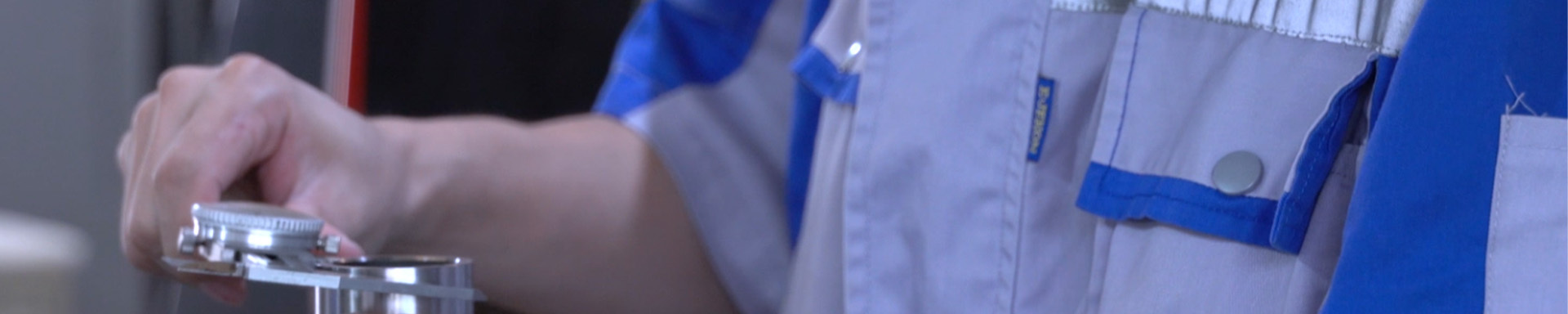
Wolframkarbid vs. Kobaltlegierung
2024-11-21 09:00Wolframkarbid (WC) ist ein Verbundwerkstoff, der in einem speziellen Verfahren aus Wolfram und Kohlenstoff hergestellt wird. Es wird allgemein für seine extrem hohe Härte und Verschleißfestigkeit gelobt. Es hat einen hohen Schmelzpunkt von 2870 °C, wodurch es auch in Umgebungen mit hohen Temperaturen eine hervorragende Leistung behält. Wolframkarbid wird häufig bei der Herstellung von Teilen verwendet, die eine hervorragende Verschleißfestigkeit und Schlagfestigkeit erfordern, wie Messer, Matrizen, Stempel und Schleifmittel.
Kobaltlegierungen sind Legierungsmaterialien, die aus Kobalt und anderen Legierungselementen wie Chrom, Nickel usw. bestehen. Sie weisen im Allgemeinen eine gute Verschleißfestigkeit, Korrosionsbeständigkeit und hohe Temperaturstabilität auf. Kobaltlegierungen weisen in Umgebungen mit hohen Temperaturen und Korrosion eine gute Leistung auf und sind daher das bevorzugte Material für Branchen wie die Luft- und Raumfahrt, die Energieerzeugung und die Chemieindustrie.
Verschleißresistenz
In puncto Verschleißfestigkeit zeichnet sich Wolframkarbid durch seine extrem hohe Härte aus, was es zur idealen Wahl für die Herstellung verschleißfester Ersatzteile wie Ventilsitze, Lager und Sägezähne macht. Kobaltlegierungen zeichnen sich jedoch auch durch hervorragende Verschleißfestigkeit aus, insbesondere bei Anwendungen, die hohen Temperaturen oder korrosiven Umgebungen standhalten müssen. Die Verschleißfestigkeit von Kobaltlegierungen ist hauptsächlich auf ihre Legierungszusammensetzung und Mikrostruktur zurückzuführen, die ihnen eine lange Lebensdauer unter rauen Bedingungen ermöglicht. Es ist auch eine häufige Wahl für verschleißfeste Ersatzteile.
Hohe Temperaturbeständigkeit
Kobaltlegierungen können auch bei hohen Temperaturen ihre gute Leistung beibehalten, was ein erheblicher Vorteil gegenüber Wolframkarbid ist. In Umgebungen mit hohen Temperaturen kann Wolframkarbid aufgrund von Wärmeausdehnung und Oxidation zerfallen. Kobaltlegierungen können ihre hohe Festigkeit und Zähigkeit sowie ihre gute Korrosionsbeständigkeit beibehalten, weshalb sie in Umgebungen mit hohen Temperaturen wie Turbinen und Motoren häufig eingesetzt werden.
Kosten
Aufgrund des komplexen Herstellungsprozesses und der hohen Materialkosten sind Kobaltlegierungen im Allgemeinen teurer als Wolframkarbid. In einigen Anwendungen können die hohe Leistung und Zuverlässigkeit von Kobaltlegierungen diese jedoch kostengünstiger machen. Unternehmen sollten das am besten geeignete Material basierend auf ihren Anwendungsanforderungen, ihrem Budget und ihren Leistungsanforderungen auswählen.
Welches sollten Sie für Ihre Anwendung wählen?
Die Wahl zwischen Wolframkarbid und Kobaltlegierung hängt von den spezifischen Anwendungsanforderungen ab. Für Anwendungen mit hohem Verschleiß oder Schneiden ist Wolframkarbid aufgrund seiner hervorragenden Härte und Verschleißfestigkeit die bessere Wahl. Für Anwendungen, die hohe Temperaturstabilität, Korrosionsbeständigkeit oder umfassende Leistung erfordern, bieten Kobaltlegierungen jedoch eine hervorragende Leistung. Bei der Auswahl der Materialien sollten Unternehmen Faktoren wie Anwendungsumgebung, Leistungsanforderungen und Kosten umfassend berücksichtigen.
Sowohl Wolframkarbid als auch Kobaltlegierungen bieten einzigartige Vorteile für industrielle Anwendungen. Das Verständnis der Eigenschaften dieser Materialien gewährleistet optimale Leistung und Kosteneffizienz. Wenn Sie sich nicht sicher sind, welches Material für Ihre Anforderungen das richtige ist, wenden Sie sich für eine individuelle Beratung an einen professionellen Werkstoffingenieur oder Lieferanten.